DRB Automotive Co., Ltd. Main menu
All Menu
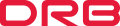
DRB Automotive has established safety as our top management policy and is committed to safety management. In addition, we are implementing various policies to create a safe working environment and enhance employee satisfaction.
DRB Automotive conducts risk assessments with the participation of all departments at least once a year to improve the safety of operational equipment and eliminate fundamental risk factors through inspections. Additionally, if new equipment or facilities are introduced, or if safety and health regulations are newly enacted or revised, we conduct additional non-regular assessments based on updated risk assessment criteria.
If a risk assessment result shows a risk level of 6 or higher, it is registered as a significant risk, and corrective actions are taken immediately in order of severity, or a risk reduction plan is established. This plan is incorporated into the business plan and operational roadmap for the year.
DRB Automotive identifies hazardous risk factors in each process, determines risk levels, and establishes mitigation measures to prevent safety accidents. The improvement measures derived from the assessments are monitored and horizontally applied across all departments. Furthermore, we strengthen our safety management activities by sharing risk assessment results between departments.
DRB Automotive has been actively eliminating internal safety hazards while also implementing health and safety initiatives for external suppliers involved in our business activities. Moving forward, we aim to enhance health and safety management capabilities in collaboration with our suppliers. Additionally, DRB Automotive conducts improvement activities to address risk factors identified during on-site inspections and provides solutions and investments through external supplier safety management evaluations.
We also work with specialized agencies to assess exposure levels to physical and chemical hazards, such as chemicals and noise, within our workplace. The results of these assessments are shared with employees via workplace bulletin boards or during regular safety and health training sessions.
Furthermore, DRB Automotive has established an automatic CO2 fire suppression system for the extrusion and vulcanization process at our Yangsan plant. A manual CO2 fire suppression system has also been installed in the coating process to enable effective early fire suppression. Through these efforts, we aim to prevent serious accidents, such as burns and toxic gas asphyxiation, caused by large-scale fires.
DRB Automotive has established standardized processes for chemical substance management, covering everything from procurement and handling to medical examinations and the management of employees with health concerns. These processes are defined through manuals, procedural documents, and guidelines.
When new or substitute chemical substances are introduced, the health and safety manager records relevant information in the Chemical Substance Inventory. This inventory includes a review of legal and regulatory requirements related to health and safety. Based on this review, DRB Automotive ensures that Material Safety Data Sheets (MSDS) are available in workplaces and that hazard warning labels are properly displayed.
Additionally, hazardous factors related to chemical handling in each process are identified and categorized. We share this information with measurement and medical examination agencies to facilitate proper monitoring and health assessments.
To maintain a comfortable and safe work environment for our employees, DRB Automotive strives to promote employee health and ensure a clean and safe workplace. Based on PPE usage and management regulations, we provide employees with appropriate personal protective equipment (PPE) and ensure that they wear it properly.
In addition, DRB Automotive supplies various PPE based on job requirements, including safety helmets, gas masks, dust masks, earplugs, earmuffs, face shields, safety goggles, and heat-resistant gloves. We also designate mandatory PPE-wearing areas and ensure employees are informed of these requirements.
To improve comfort and usability, DRB Automotive continuously enhances the convenience and performance of PPE used in the workplace. Furthermore, we implement a Hearing Conservation Program and adhere to health and safety standards, including a Confined Space Health and Safety Program, to ensure compliance and protect employees' well-being.
DRB Automotive conducts various inspection activities to ensure the safety of our employees and all visitors. We continuously take action to improve risk factors identified through these inspections.
Joint labor-management health and safety inspections are conducted quarterly, and the findings are communicated to the relevant department representatives. Improvement plans are then established, and their implementation is monitored. The Occupational Health and Safety Committee reports the results of these efforts to the CEO, the decision-maker who serves as the Health and Safety Management Officer.
To ensure that employees work in a healthy and safe environment, we conduct internal evaluations to assess and enhance our occupational safety and health management capabilities.
Additionally, we conduct regular fire safety inspections to maintain optimal fire protection conditions and prevent casualties from fires. We also hold an annual joint fire drill in collaboration with the local fire department.
Exposure levels to hazardous substances during work processes are measured and shared with employees, ensuring that harmful substances remain within permissible limits. For work processes with a high risk of musculoskeletal disorders, regular hazard assessments are conducted, and process improvements are implemented accordingly.
Furthermore, DRB Automotive actively motivates employees to engage in health and safety management through initiatives such as the Zero-Accident Team Reward System and safety awareness campaigns. We also conduct regular safety inspections of hazardous machinery and equipment, including industrial robots, pressure vessels, cranes, rollers, and lifts, to provide a secure working environment.
Before introducing new equipment or processes, DRB Automotive develops and implements a Hazard Prevention Plan to ensure worker safety from the outset.
DRB Automotive recognizes that raising employees' safety awareness is the most crucial factor in achieving our core vision of a zero-accident workplace and health-conscious management. To foster a strong safety culture, we implemented various environmental, safety, and health awareness campaigns.
To reinforce awareness of serious industrial accidents, DRB Automotive organized a safety slogan contest focused on major accident prevention and fire safety awareness. Employees were encouraged to participate actively through incentive rewards for winning entries. The best slogans were selected as the official company-wide safety mottos and displayed at the entrance to instill a shared sense of safety consciousness among all employees.
Additionally, DRB Automotive utilized meal breaks to show industry accident prevention videos and share key safety case studies, raising awareness of workplace hazards and reinforcing the importance of accident prevention.
DRB Automotive has established a health and safety policy and continuously educates all employees to ensure compliance. We also operate an emergency response system to take immediate action in case of accidents.
To strengthen employees' emergency response capabilities, DRB Automotive conducts scenario-based emergency drills and training programs tailored to various disaster types, including industrial accidents, fires, environmental incidents, and natural disasters. Additionally, we provide customized safety training based on job roles and hierarchical levels to enhance employees' safety competencies.
For employees handling hazardous chemicals, Material Safety Data Sheet (MSDS) training is conducted in advance, ensuring they fully understand the hazards and risks associated with the chemicals they work with.
Every year, DRB Automotive conducts mandatory legal safety training for employees and external suppliers to raise safety awareness and minimize risks. We support hazardous chemical handling training for external supplier workers to ensure compliance with safety regulations and prevent workplace hazards.
Training | Target | Training Period (Hours) |
---|---|---|
Emergency response training in case of accidents | Supervising manager, Office workers, Production workers | 2024.10.7/10.14(2 Hours) |
Emergency (fire) response training | Supervising manager, Office workers, Production workers | 2024. 9. 27/10.2(2 Hours) |
External training for supervising managers | Supervising manager | 2024.1.2~2024.12.19(16 Hours) |
DRB Automotive is committed to fostering a health-friendly workplace culture and environment. We continuously strive to create a supportive organizational culture and work environment that prioritizes employee well-being. By encouraging employees to take an active role in managing their own health, DRB Automotive is moving forward as an exemplary company in health-conscious management practices.
DRB Automotive conducts annual general health checkups and comprehensive health examinations every two years. Additionally, we provide specialized health checkups tailored to specific hazardous factors to ensure employees' well-being.
To enhance workplace safety, DRB Automotive evaluates the working environment for on-site employees twice a year. Based on these assessments, we implement continuous improvement measures to create a safer and healthier work environment.
DRB Automotive operates personalized health support programs and a healthcare center to promote employee well-being. These programs include customized exercise training, body composition management, oral health care, walking programs, sleep health support, and smoking cessation initiatives.
Additionally, we have established an employee health management database to track progress, evaluate outcomes, and support self-care, ensuring a tailored approach to employee health management.
Program | Description |
---|---|
Customized exercise education program |
|
Anti-smoking program |
|
Mental health promotion program |
|
DRB Automotive conducts preference surveys to understand employees' needs and selects programs accordingly before implementing any program. After completion, we collect participant feedback to continuously improve program quality and ensure a more effective and engaging health management experience.
Unit: EA
Type | 2022 | 2023 | 2024 | Notes |
---|---|---|---|---|
Conveyor | 1 | 14 | 1 | |
Industrial robot | 5 | 1 | 1 | |
Roller | 2 | - | ||
Crane | 2 | - | ||
Pressure vessel | 9 | 34 | 9 | |
Lift | 1 | 1 | ||
Injection molding machine | 9 | 2 | 9 |
Unit: Species
Type | 2022 | 2023 | 2024 | Notes |
---|---|---|---|---|
Number of harmful agents measured | 15 | 27 | 35 | |
Number of agents exceeding the exposure standards | 0 | 0 | 0 | |
Number of agents less than 50% of exposure standards | 15 | 25 | 33 |
Unit: Person
Type | 2022 | 2023 | 2024 | Notes |
---|---|---|---|---|
Number of employees participating in the exercise (walking) program | 19 | 49 | 32 | |
Number of employees participating in the fitness program | 17 | 43 | 61 | |
Number of employees participating in the musculoskeletal health program | 13 | - | - | No activity for 2023, 2024 |
Number of employees participating in the anti-smoking clinic | - | 17 | - | No activity for 2024 (Insufficient number of participants) |